From Concrete Slabs to Tailored Solutions: The Evolution of Flooring at Godwitt
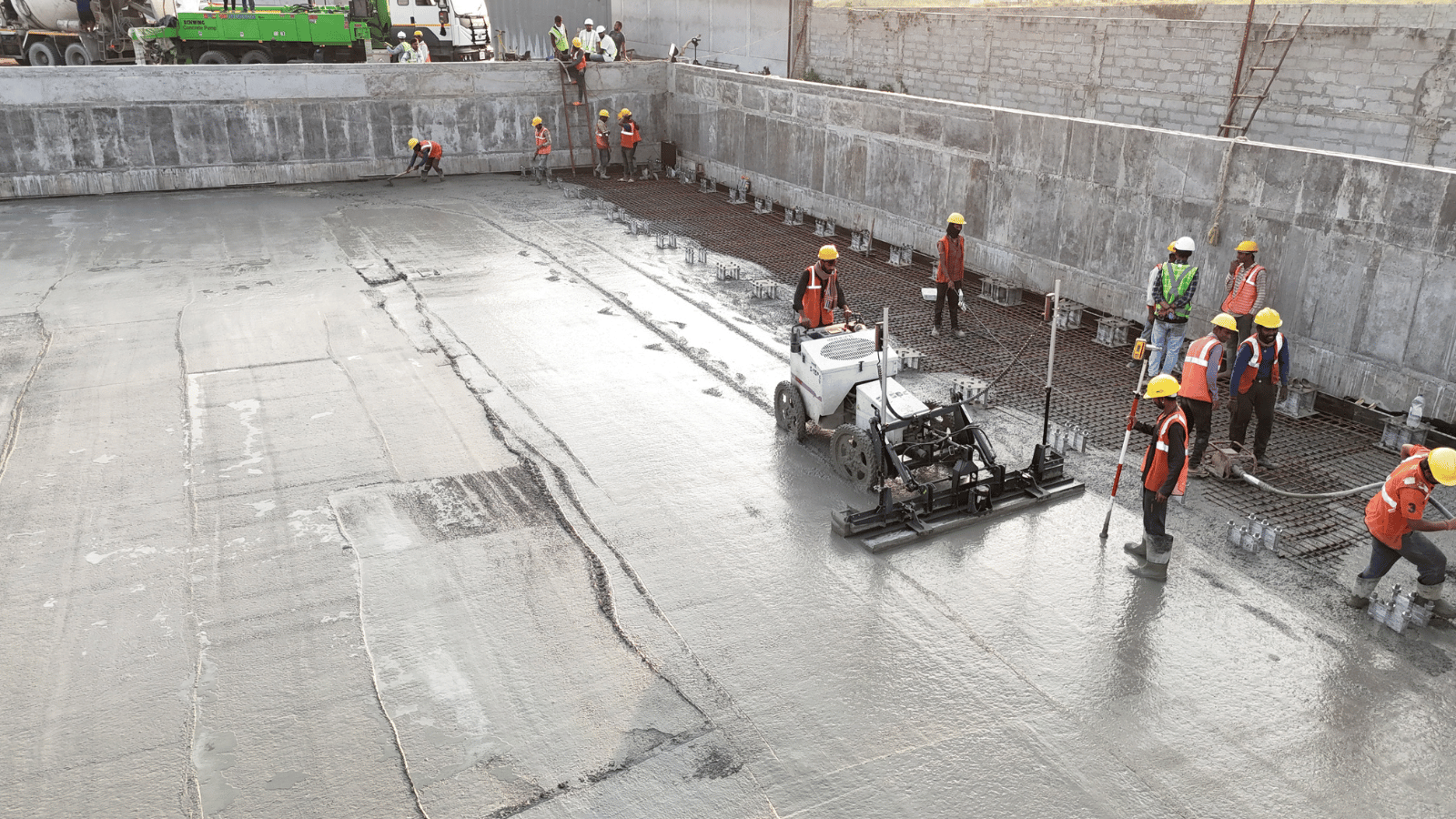
In the ever-evolving landscape of industrial facilities, floors have traditionally been viewed as functional foundations rather than strategic assets. However, that perception is rapidly changing, especially at Godwitt’s facilities. For us, flooring is emerging as a focal point for innovation, performance, and long-term sustainability.
From withstanding the workload of high-capacity machinery to ensuring seamless movement across automated storage and retrieval systems (ASRS), resilient flooring plays a critical role in operational performance. Godwitt recognised this early on, and through smart interventions, it is now changing how industrial floors are designed, constructed, and maintained in our facilities.
Flooring Innovation at Godwitt:
Early Challenges with Traditional Flooring
In the early days of construction, we realised that traditional methods were shaping the flooring infrastructure. While these techniques had been widely used across industries, they also presented several notable challenges:
- Inconsistent load-bearing capabilities
- Surface cracking due to material fatigue and unregulated temperature changes
- High lifecycle maintenance
- Extended construction timelines
- Overdependence on skilled labour with limited innovation
These issues created operational friction for facilities aiming to scale manufacturing or optimise their warehouse or cold storage operations. It became clear that more than durable concrete was needed; the industry required a new construction methodology emphasising project-specific precision and operational durability.
The Steel Fiber Reinforcement Breakthrough
Enter steel fiber reinforcement, a turning point in the flooring evolution at Godwitt. This method involved integrating steel fibers into the concrete mix during floor construction. This single change dramatically elevated performance by reducing microcracking, increasing surface strength, and enabling the floors to carry heavier loads.
With its ability to create a seamless floor structure, steel fiber reinforcement enhanced the flooring's integrity throughout each facility in the park. The result was a clear drop in repairs, improved tenant satisfaction, and accelerated delivery timelines.
Standardising with FM2 Specifications and Vendor Partnerships
To complement its structural improvements, Godwitt adopted FM2 floor specifications across its industrial spaces. These standards guarantee flatness and levelness critical for operations relying on mobility, storage precision, and automation, such as ASRS technology.
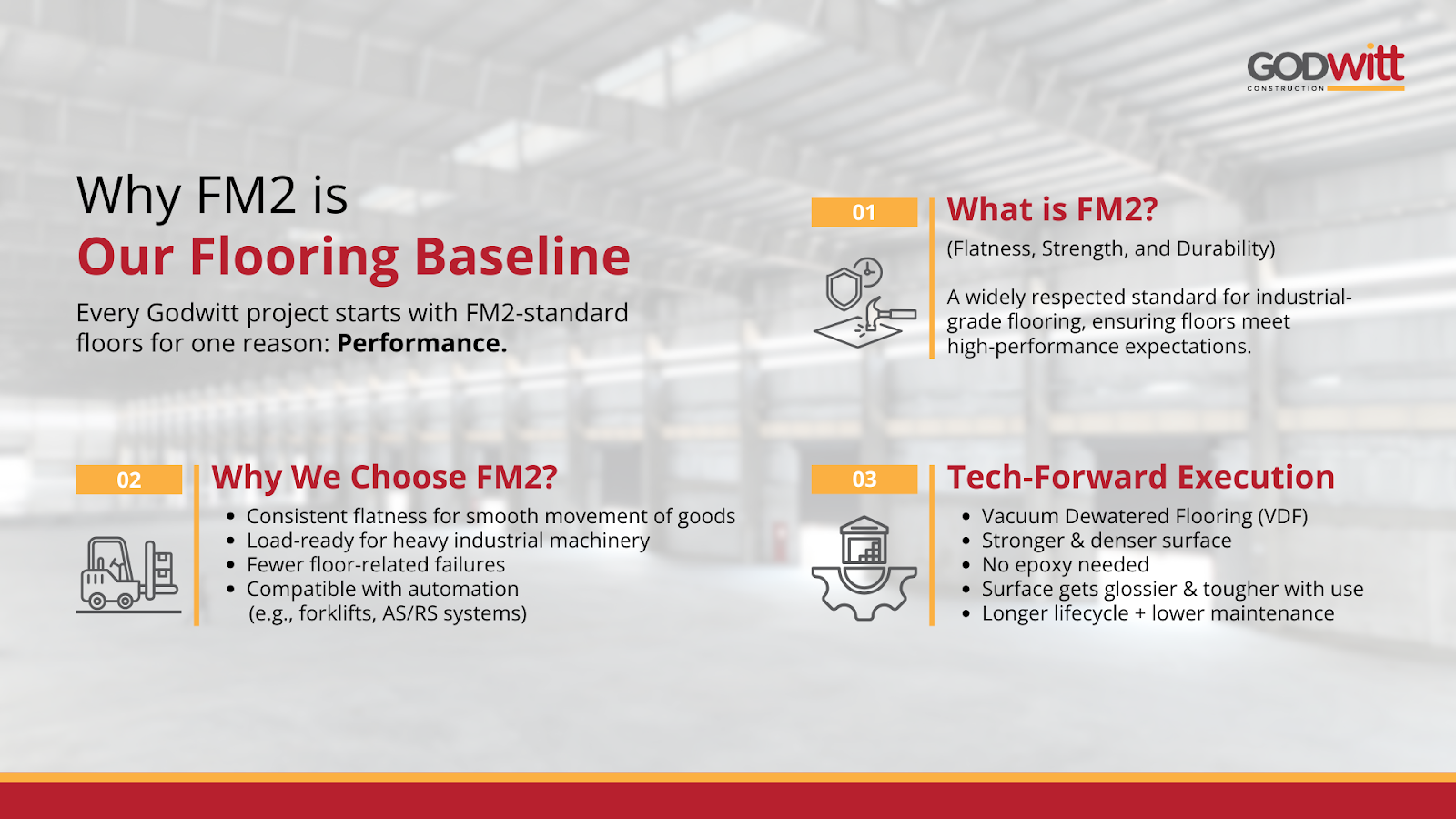
Unlike epoxy-coated floors that require periodic maintenance and have a limited lifecycle, VDF techniques ensure that excess water is withdrawn after the flooring pour. The outcome is a denser, glossier, and steadily hardening floor that strengthens with time and use. For every facility, this means flooring that doesn’t just function, it improves lifecycle performance without recurring investment.
Anywhere from 1 million square feet to individual industrial units are being laid out using this method across strategic park areas at Godwitt’s campuses, streamlining construction and long-term efficiency.
An Occupier-Centric Pivot: No Preset Floors
Another major shift was how flooring strategies aligned with business-specific operations. Initially, a one-size-fits-all approach dominated floors prelaid in anticipation of occupancy, assuming uniform operational needs.
However, real-world use quickly demonstrated that this created unnecessary retrofitting and compromised floor integrity.
Godwitt realigned its project model to focus on the occupier. Now, no flooring is constructed until after a lease is finalised and the operational requirements are clarified. Once a client is onboarded, Godwitt’s engineering team collaborates on a tailored flooring plan, mapping out:
- Load charts and machinery placement
- Zones of chemical exposure or heat generation
- Movement paths, storage containers, racking outlines
This occupier-first framework allows our teams to implement exactly what is needed with zero waste. The result is greater alignment with our occupiers’ business operations, higher occupier satisfaction, and a smoother transition from construction to operation.
Innovative Flooring Customisations: Built for Every Industry
We focus on modular, tenant-specific designs that accommodate diverse industries. Four major custom flooring solutions have emerged over the years to meet modern needs:
1. Machine Foundation Flooring
Designed to support static machinery like CNC lines or plastic injection moulding equipment. Load analysis and vibration-dampening structures are incorporated during construction.
2. Anti-Static Flooring
Critical for industries like electronics or chemical processing, where static discharge can be disruptive or dangerous.
3. Epoxy Coating
Ideal for cleanroom industries such as pharmaceuticals or food processing, where cleaning and hygiene are paramount.
4. Densified Floors
These deliver superior abrasion resistance for heavy-duty warehouse storage zones and logistics corridors where forklifts and mechanised load movement are constant. Each type ensures businesses can scale operations without disruption caused by flooring failure, unlocking higher productivity and better safety over time.
Strategic Maintenance Support Throughout the Lease Lifecycle
Flooring isn’t just built; it must be sustained. Godwitt has implemented a long-term maintenance ecosystem that tracks performance and supports occupiers at every operational milestone.
The support services include:
- Periodic visual and sensor-based inspections
- Crack detection and remedial flooring solutions
- Surface polish and densifier maintenance
- Seamless coordination with occupier transitions or layout upgrades
This strategy adds long-term value, lowers downtime, and ensures every structure meets required specifications throughout its lease.
As India’s industrial real estate trend grows, this attention to aftercare will become a defining factor separating world-class developers from commoditised offerings.
Flooring as a Strategic Asset: Insights, Sustainability, and Innovation
At Godwitt, floors aren’t just poured; they’re engineered. Each slab contributes to an industrial space that scales, adapts, and accelerates growth. This transformation is not just a construction evolution but a strategic thought.
Godwitt’s flooring strategy integrates:
- Sustainable construction practices such as low waste from over-pouring
- Insight-based planning informed by each occupier’s workflow
- Use of smart materials, like steel fibre and VDF techniques, to maintain long-term structural integrity
All this innovation keeps Godwitt at the forefront of the industrial development landscape, empowering occupiers with versatile and fit-for-purpose infrastructure that grows with them.
At Godwitt:
From supporting ASRS systems to handling temperature variations and high footfall, flooring plays an essential role in overall operational efficiency. At Godwitt, this aspect of infrastructure is no longer viewed as a routine construction step but as an integral part of enabling reliable and future-ready industrial spaces.
By aligning flooring solutions with occupier needs, incorporating techniques like Vacuum Dewatered Flooring (VDF), and ensuring consistent maintenance support, the goal is to create spaces that are both practical and adaptable over time.
Across locations like Nana Borsara and other industrial belts, Godwitt continues to focus on durability, efficiency, and long-term usability in its developments. Whether the requirement is for manufacturing, warehousing, or temperature-controlled storage facilities, the approach remains centred on well-planned, technically sound execution.
Why to sign up for a newsletter
Open